Backfill of Tailings to Underground Workings
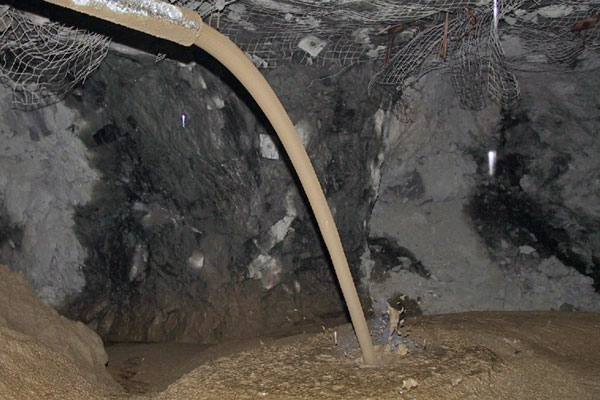
Figure 1: Filling of an Underground Stope (© Barrick Gold)
Introduction
Tailings can be stored below ground in previous worked out voids. The tailings are generally mixed with a binder, usually cement, and then pumped underground to fill voids and help support an underground mine. For example a ‘room and pillar’ mining operation that uses backfill will be able to extract the insitu pillars containing ore. This is possible due to the cemented backfill acting as a support and preventing heading collapse and problems with subsidence. The backfill tailings are generally mixed on the surface with the cement in a small processing plant and then piped either down a decline, shaft or surface borehole(s) into the area of the mine that requires backfilling.
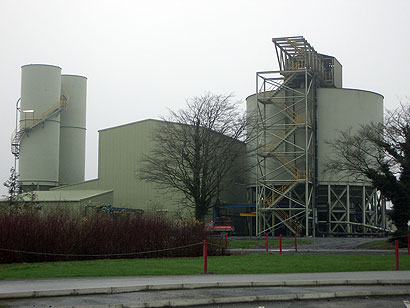
Figure 2: Paste backfill plant with deep cone thickener, Lisheen Mine, Ireland (© Jon Engels)
- Advantages:
- The tailings are stored underground and thus prevent surface disturbance. This is more environmentally friendly as areas of land don’t have to be used for a surface tailings storage area. Problems associated with dust generation, visual impact, contamination of surface water courses and inundation risks associated with tailings facility failure can be mitigated using backfill
- Ore rich pillars and supports can be extracted
- The backfill helps to support the mine
- Backfill reduces the risk of rock bursts occurring as pressures are not focused on pillars and supports
- Improves the ventilation circuit in the mine
- Prevents roof falls from blasting (Air Over Pressure (AOP))
- Binders help to minimise groundwater contamination.
- Oxidation rates for pyritic tailings can be reduced (Acid Rock Draiange (ARD) development)
- Increased water recovery from the tailings prior to storage when compared to conventional disposal (majority of cases)
- Disadvantages:
- High costs, particularly if binders are used
- The tailings need to be highly dewatered usually to paste consistency (high OPEX for production and transport of high density tailings)
- Expensive positive displacement pumps are usually required for high density tailings discharge (some manufacturers having high lead times)
- Hold ups in extraction and mine development strategies
- Risks of liquefaction of the tailings if saturation levels are high, and a trigger (seismic vibration) are present. Barricade walls usually required, particularly in underground stoping methods.
- Seepage of tailings effluent into groundwater, thus possible contamination
- Extra manpower and equipment mangement (operation of an independent plant required)
- Ore dilution from poor quality fill placement or extraction management
Binders (cementing) help to prevent groundwater contamination as the backfill experiences chemical and physical characteristic changes. For pyritic tailings the cement will reduce oxidation and acid generation of the fill, thus resulting in reduced mobilisation of metals. This is particularly useful if an underground void is below the water table, as when pumping ceases the cemented fill will be in direct contact with groundwater. Problems with fill migration, liquefaction and slump are prevented.
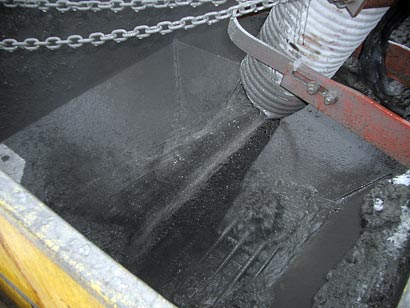
Figure 3: Pipeline from the plant depositing backfill tailings down a surface borehole (© Jon Engels)
Problems with backfill
There are many problems with backfill. The main issues being:
- Plugging of pipe line – A big problem if binders are used as the pipeline may need replacing
- Borehole plug – If the backfill is pored down a borehole there is a chance it can get plugged. Redrilling may be required or an alternative borehole required
- Backfill sloughing – The backfill forms a crust that can shed allowing fresh backfill to migrate
- Pipe line burst due to high pumping pressures
- Bulkhead failure (barricade)
- Pipe hammering
- Liquefaction of the backfill
- Backfill segregation
- Plugged sump
- Rat holing
- Pump failure
Types of backfill used in underground mines
There are four types of backfill used:
- Paste backfill:
- Paste backfill is similar to surface paste deposition. The tailings are dewatered to generally >65% solids (by weight) and pumped underground, generally by positive displacement pumps. The paste has a homogenous appearance and produces a measurable slump (visible when released from a cone shaped slip mold (Abrams)). When the paste is deposited underground there is little to no bleeding of the contained water.
- Hydraulic sand fill:
- Hydraulic sand fill is used when the tailings are cycloned to produce separate slimes and sand fractions. The slimes are disposed due to their poor permeability and are generally stored in a surface storage facility. The sands are hydraulically pumped underground into the voids and can be mixed with binders if need be. As the sands settle and consolidate the excess water is bled off or lost through seepage.
- Cemented fill:
- Cemented fill consists of tailings and waste rock deposited in underground voids. It is used when storage of waste rock is required and the excess void spaces need filling. Tailings mixed with cement can be poured over the waste rock to fill and bind the voids. This is useful when low volumes of cement slurry are required (cost implications) to bind the backfill.
- Dry rock fill:
- Dry rock fill is rock waste, surface sands, gravels, or dried tailings. The fill is either dropped down a raise, or tipped into an open stope by a Load Haul Dump (LHD) or dump trucks. Dry rock fill is most suited for the cut and fill mining method.