Laboratory and Pilot Plant Programmes
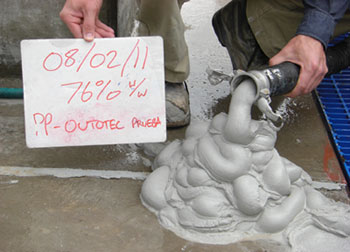
Figure 1: Paste tailings thickening trial (© Jon Engels)
Pilot Tailings Thickening
Over recent years there has been an increased demand to run pilot scale tailings trials either as part of metallurgy testing or on a semi-industrial scale normally located at an existing mining operation. These pilot plants are fundamentally focused on thickening trials to determine the ability to increase the solids concentration of the tailings towards or beyond paste while defining:
- Full scale thickener type and sizing (high compression, high rate, deep cone)
- Feedwell and underflow design (optimising inflow and underflow draw)
- Feed dilution optimisation
- Optimum flocculant type and dosing rate
- Rake design and rotation speed
- Improved confidence in capital costs (number of thickeners required and sizing)
- Improved confidence in operational costs (power draw, flocculants, water consumption)
These larger pilot scale programmes normally follow from benchtop sedimentation and thickening trials to determine the ‘potential’ limits of thickening a particular type of tailings. Quite often the results from large scale pilot plants are different and provide an improved realistic approach to defining thickening limitations for a full scale operation.
Occasionally there are contractual obligations with vendors set out by mineral operators to ensure that any equipment performs as intended. Therefore it is in the interest of thickener vendors to promote pilot and demo plant trials to reduce operational risk and define an installed system with improved levels of confidence.
Types of Pilot Plants
There are several types of pilot plant testing considered in tailings handling and storage facility design. These are summarised as follows:
- Pilot Thickening Trials:
- Limit Testing – Onsite pilot thickener trials using a truck mounted or small scale thickener (typically up to 5 tonnes per day) operating for a short period of time, primarily to determine limitations of thickening an existing tailings feed. These styles of trials are driven by thickener vendors to adopt high rate, high compression or paste thickening technology.
- Design Testing – A pilot thickener operating for a prolonged duration to determine design parameters such as flocculation optimisation, dilution requirements, feedwell design etc. These thickening trials are sometimes operated in association with other processing plant design tests (e.g. cycloning and separation of tailings feeds into two streams, screening and grinding variations).
- Demo Plant – A demo plant is usually a full scale thickener installed at an existing mining operation and run in parallel to the existing thickening trains. The demo plant could be a deep cone thickener producing high density tailings that discharges into the same delivery system as the already installed conventional thickeners (thus allowing dilution and prevention of associated transportation issues). This demo thickener is effectively a full scale trial for refinement of the future installed design for the specific properties of the tailings feed while demonstrating functionality to a mineral operator. The idea is that all thickeners will later be replaced with the demo plant design to allow a mine to produce tailings at a higher concentration for the full production throughput (sometimes a progressive changeover to reduce operational risk).
- Tailings Related Trials:
- Metallurgical Trials – Tailings produced from metallurgical trials are usually of low volume (particularly if core samples have been used). However, the volume can be sufficient for laboratory based testing and can provide a good indication to behavioural properties of the tailings for larger pilot scale development or feasibility design of a tailings storage facility. Beach slope prediction tests (non-laboratory) can be performed if the metallurgical tests produce a sufficient volume of testing. However, some of the key laboratory trials conducted from metallurgical derived tailings are:
- Classification (e.g. PSD, SG (liquor and solids), Atterbergs).
- Sedimentation and air drying.
- Permeability and consolidation testing.
- Benchtop thickener testing (e.g. Superflo or Vietti).
- Flocculant characterisation and dosing.
- Tailings Pilot Plant – A purpose built pilot plant to assess thickening, transportation and deposition of tailings, normally for a range of solids concentrations. These plants vary in scale but normally incorporate a small pipe loop and a discharge flume to predict beach slope values. Large pilot plants (such as the 70 tpd CODELCO thickened tailings pilot plant) considered three different beach slope prediction methods, two large pipe loops and a large deep cone pilot thickener to determine design parameters for HDTT storage design.
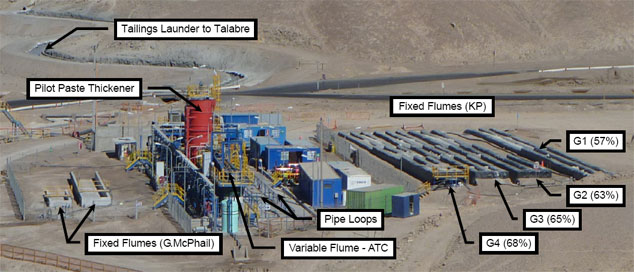
Figure 2: CODELCO Thickened Tailings Pilot Plant (taken from Engels et al, 2012)
Parallel Testing Programmes
The advantage to a pilot thickening trial is that parallel tests associated with transportation and deposition of tailings can be conducted relatively easily. A pilot or demo thickener is producing tailings at a range of concentrations that are being considered for the full scale operation through optimisation of the trial thickener. These tailings can be considered for other testing such as:
- Laboratory Trials
- Basic classification and characterisation tests can be performed for a range of solids concentrations and easily rerun based on thickener optimisation during the course of the trial (e.g. different flocculant doses, shearing effects).
- Transportation Characterisation
- Pipe loop(s) can be developed to assess the transportation behaviour of the tailings for varied concentrations. For example, head losses associated with the pumping of the tailings from the full scale thickener(s) to the points of discharge within the final tailings storage area can be determined. Recommendations regarding limitations of pumping (e.g. conventional centrifugal pumps), power costs, system capital expenditure and system design can be made.
- Beach Slope Characterisation
- The incorporation of beach slope prediction flumes, such as those of Gordon McPhail and ATC Williams. Flumes can be constructed next to the thickener and be programmed to receive tailings at a range of flow rates either directly from the thickener underflow feed or better from an intermediate holding tank.
- Deposition Characterisation
- The incorporation of trial cells such as those designed by Jon Engels to determine variations in water recovery (supernatant and underdrainage), drying time, in situ density with time, pore pressures and how these behaviours are influenced by deposition layer thicknesses. These tests can assist to optimise tailings facility design and disposal operation to maximise water recovery.
Tailings Stream Separation
Introduction
With the requirement to reduce water consumption, some mines are looking at alternatives to maximise water recuperation from the tailings stream. Although paste and dry stacking essentially achieves this goal through thickening and filtration, the tailings properties themselves may physically limit the higher solids concentrations obtainable (e.g. thickener limitation, blinding of filter cloths with fines). For thickening, this can be determined through the thickener Limit Testing programmes as mentioned previously. However, now there is a trend where separation of a single tailings stream into two may recover more water, thus changing the properties (and volume) of the tailings that are later thickened or filtered, or a combination of both.
Hydrocyclones
Traditionally hydrocyclones were integrated in tailings storage design to separate a single tailings stream to provide a coarse fraction of tailings to use as an embankment construction material, with the fines deposited within the containment area. This is still frequently practiced for conventional tailings storage utilising the crest cyclone or the hydraulic cell construction technique.
In recent times, the use of hydrocyclones has been considered in an effort to optimise thickening of tailings to higher solids concentrations. For example, the coarse fraction (underflow) produced by a series of hydrocyclones may have a high solids concentration beyond that feasible to be transported hydraulically. The natural low fines content of this coarse product therefore makes filtration attractive to recover more water and allow deposition in a dry stack style tailings storage facility. The overflow (fines) from the cyclones (the solids volume of which is usually less than the underflow produced) is therefore thickened to a high density and deposited in a containment facility. A further option is to recombine the coarse and thickened fines as a single tailings stream to be hydraulically or mechanically transported to the final storage area. These processes sound feasible, but many mineral operators and tailings designers need to consider the following:
- Hydrocyclones require high amounts of dilution to operate effectively. This water has to be managed and piped to the hydrocyclone banks. It is unlikely to be a closed loop direct from any thickener due to losses in the tailings (i.e. make-up water required).
- High feed pressures (around 20 PSI) are required to operate hydrocyclones effectively (i.e. booster pumps required). This increases operational costs.
- Variability in underflow and overflow production volumes (normally influenced by variations in feed pressures and inner cyclone wear).
- A two stage cycloning process maybe required where the underflow from the first stage may require additional dilution and further cycloning to obtain a manageable underflow product (i.e. low fines content).
- Two tailings streams require handling and transportation:
- Coarse (underflow) - To be filtered (if necessary) and transported to a final storage area, or recombined with the thickened fines.
- Fines (overflow) - To be thickened and pumped to a final storage area (with or without the coarse fraction added).
- Additional costs:
- Installation and operation of hydrocyclones.
- Additional pumps to increase feed pressures to the hydrocyclones (as well as return dilution water pumps).
- Additional pipework and tanks for dilution requirements (including potential make-up water requirements).
- Design, construction and operation of two tailings storage areas (if necessary)
Some of the benefits of tailings stream separation are as follows:
- The entire tailings stream may not require thickening (generally only the fines fraction) leading to a reduced reliance on thickening technology to recover water from the tailings. Also the number of thickeners will reduce.
- Higher solids concentrations could be produced by the thickeners when utilising a narrower banded granular distribution of tailings.
- Combining a filtered (or unfiltered) coarse product (underflow) from the hydrocyclones with the thickened fines may produce an overall higher solids concentration of tailings than what could be produced via limited thickening of the single tailings stream.
A detailed trade-off study investigating the feasibility of separation for a particular tailings type together with a series of handling options should be conducted. Any potential increase in water recovery needs to be assessed on a cost basis together with the associated capital and operational expenditure of operating hydrocyclones. Another important consideration is the risk associated with complicating an easier manageable single stream tailings discharge system.
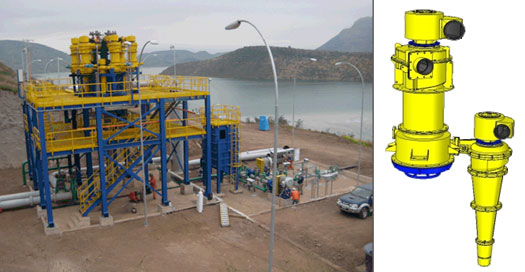
Figure 3: Hydrocyclone house for separating a tailings feed using the Re-Cyclone© hydrocyclones (right) (courtesy of Weir Minerals)
Feasibility and Testing Programmes
Based on the idea of separating the feeds, the first step is to determine the hydrocyclone splits. This can be achieved through computer modelling knowing a few basic parameters of the associated tailings, and later through metallurgical trials or an onsite pilot testing programme. These testing programmes can be integrated as part of any tailings pilot plant to improve the confidence that splitting the tailings into two streams may recover more water and reduce the reliance on thickening the full throughput of the processing plant.
Closing Comments
The design of a pilot plant can be complex with an expectation from a mineral operator that the plant will operate as intended once construction has been completed. The reality is that it is a “pilot” and modifications need to be made to be able to operate the plant effectively and efficiently whilst being able to measure intended design/operational parameters easily and with a high degree of confidence. Tailings design consultants and mineral operators should consider a wide range of tests as part of any pilot plant design. For example, a pilot thickener trial that is focused on determining thickening limitations of a feed can easily incorporate flumes to assess beach slope variations using the underflow feed from the thickener. For a large thickener demo plant, a series of small hydrocyclones could be incorporated to assess the variations in thickener performance for different tailings gradings. The coarse fraction could be used in filtration trials or in a pipe loop (with thickened slimes) to determine the transportability of the two independent waste streams generated. The list goes on…